Lean Methodology: Transforming Your Business
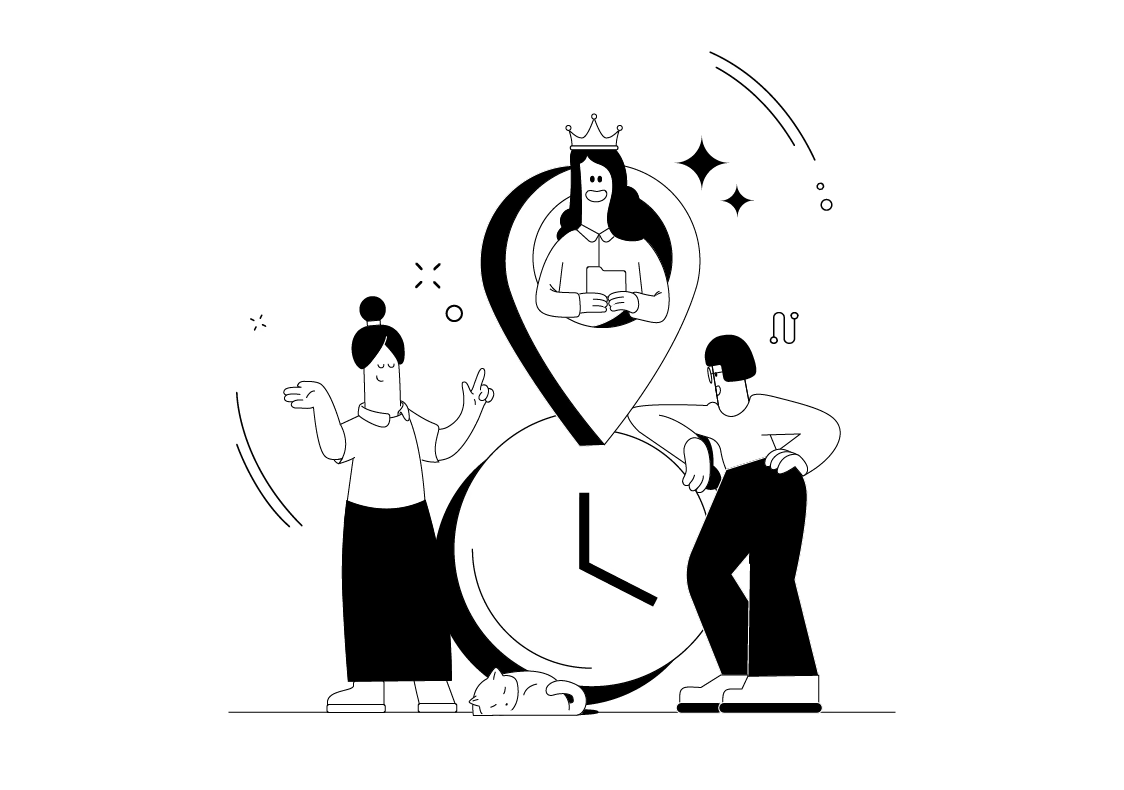
The Lean methodology is best described as a mindset that shifts the focus of the entire organization to customer demands and makes sure no time or resources are wasted. The result of its application is an efficient process that only gets more successful over time.
What is Lean Management?
By definition, Lean management is a business approach aimed at making the manufacturing process as wasteless as possible. It’s a philosophy based on several principles and pillars that define the approach that was born in the Toyota factories. Lean methodology, on the other hand, is the set of tools used to implement that approach. The methodology has been used worldwide for decades in the manufacturing industry, software companies, and other business branches.
Pillars of Lean Methodology
The Lean methodology isn’t just a ready-to-use recipe for eliminating waste and making companies more efficient. It relies on Lean thinking which is based on two pillars: continuous improvement and respect for people. Continuous improvement, also known as Kaizen, means constantly looking for ways to change processes and operations so they become better. When this way of thinking is introduced, teams will constantly implement small improvements to their work and increase the output’s quality.
Respect for people is a lesson all companies should learn. It teaches that all employees matter regardless of their role and rank, as well as their opinions. Distributing ownership to all organization levels leads to team members caring more about what customers think and taking up more responsibilities.
After various companies tried to apply the Lean philosophy to their processes, the methodology received some negative feedback. In 2001, the president of Toyota published a book on Lean principles that focused on respecting people, highlighting the human side of workflows. It put an emphasis on flow and pull—producing only what’s demanded without any interruptions or bottlenecks in the value stream.
The Lean approach strives to build quality and reminds teams to solve issues before they become too serious to handle. The goal is to catch defects as soon as they appear, rather than wait for quality control. This helps to develop a culture of continuous improvement as the team works on developing the product. The Lean approach helps project managers create a long-term vision and make important decisions based on the long-term effects rather than trying to reach short-term goals.
History and Evolution of Lean Management
Lean management originated in the Toyota factories of post-WW2 Japan. This company went from bankruptcy to a successful multinational automaker. The key to this miraculous change was the many restrictions the Japanese manufacturers faced, which forced them to find a more functional way to produce cars. Toyota managers learned some lessons in America and applied them to their processes. During the 1950s, they implemented two core methods: just-in-time and automated quality control. The goal was to eliminate all types of waste and produce only what was requested.
In the 70s, the Toyota approach spread to other automakers worldwide who were interested in replicating their success. The Lean principles were applied in other industries as well.
In the 90s, there was an expansion of Lean system to service industries. The operations management improves efficiency and productivity, while the elimination of waste is closely related to quality management. Several books were published that popularized the ideas behind Lean, making them more accessible to all types of companies.
The 21st century brought to the surface the importance of project management in improving project efficiency and speeding up delivery times, as well as removing any obstacles during processes. The principles of Lean production were combined with other methodologies so any kind of team can adopt the best approach to their needs and complete projects successfully.
Basic Lean Principles
The five basic principles of Lean manufacturing include identifying value, mapping the value stream, creating flow, establishing pull, and seeking perfection.
The main idea is to find out what customers value most so the company doesn’t waste time or resources producing what’s not needed, which can be done following the basic principles of Lean. Mapping out all processes and information flows allows managers to identify waste at every step and eliminate it, creating an uninterrupted flow without bottlenecks. Pulling means producing by request. Companies don’t manufacture products or provide services that are not demanded by customers. Finally, the Lean process commands continuous improvement. All employees should constantly try to find ways to make the process even better and eliminate waste where possible using these basic Lean principles.
Seven Wastes of Lean
Lean gets its name because it helps companies get rid of waste and become “leaner”. The seven types of waste in the Lean management theory are overproduction, waiting, defects, overprocessing, unnecessary motion, excess inventory, and unused talent. “Muda” is one of the key concepts in Lean management. Lean strategy helps the organization reduce waste and improve productivity. These are the seven types of waste in Lean:
Overproduction— Producing more than the demanded quality can lead to excess inventory or lower quality standards.
Waiting— An uninterrupted process without bottlenecks is crucial for the Lean flow. Waiting for input, materials, people, or transport is a waste of time and can cause serious issues and costs in the manufacturing chain.
Defects— Lean emphasizes automated quality control so defects are spotted right away. If they slip by unnoticed, the company could end up facing returns from unsatisfied customers or scrap.
Overprocessing— Wating resources without adding value is a common slip in many industries. Some processes are carried out because “it was always done that way” and steal time and effort that could be invested more productively.
Unnecessary motion— Movements of equipment, materials, or people that don’t add value should be eliminated. Sometimes, this type of waste is easy to spot, but sometimes it takes an unbiased set of eyes to notice it.
Excess inventory— Stacking up excess inventory can increase storage costs or even lead to the company keeping outdated items that will only be thrown away, wasting the effort and resources used to produce them.
Unused talent— This is the only waste not strictly bound to the production process but no less important. It’s crucial to know which skills your employees possess and how to make the most of them. Wasting someone’s talent by making them work in an ill-suited position is a form of waste that will reveal itself long-term.
Lean Methodology Tools
Lean provides a set of tools that makes implementing these specific principles and pillars easier for any type of team. The list of these tools is long and we’ll go over the most commonly used ones.
Value Stream Mapping (VSM)— A visual tool that helps managers break the process into steps and identify waste so it can be eliminated. It’s also a great tool for optimizing processes and spotting potential bottlenecks.
5S Workplace Organization— This very simple tool is easy to remember:
Sort: remove waste
Straighten: organize what’s left
Shine: maintain the work area clean
Standardize: set in place workspace standards
Sustain: apply, maintain, and improve the 5S steps
Total Productive Maintenance (TPM)— This approach emphasizes the importance of maintaining all equipment proactively and preventatively. The operators are encouraged to share the responsibility of the proper machine functioning, so maintenance staff isn’t as employed. This can help prevent severe malfunctions and defects as well as eliminate the need to wait for maintenance.
Statistical Process Control (SPC)— This method is strictly tied to the production process as it monitors manufacturing and measures and controls the quality. SPC shows how consistent is the performance of a product. Its goal is to reduce scrap, returned items, and reworks.
Lean Thinking
Lean thinking is a business philosophy that influences decision-making, mostly in the manufacturing industry. While one side of the coin is Lean tools, the other is Lean thinking. Lean principles and pillars help teams think in the proper way and apply the methodology correctly. By applying the five basic principles at all company levels, waste can be significantly reduced, and all processes can be much more efficient.
It’s crucial to let all employees know that they should focus on customer demands. Once everyone understands that all activities must serve to meet customer needs and provide what they value most, the shift in the mindset will allow them to identify business areas that can be improved. Respect for people means valuing the opinions of all team members. Once they recognize that, they’ll be more free to express their opinions.
Lean vs. Agile
Lean and Agile share many similarities and are often confused with one another because of their flexibility, adaptability, and focus on the end user. We’ll explore some of the differences that set them apart. Find out all the details on the Agile methodology and its manifesto.
- Focused on eliminating waste
- Focused on delivering working software quickly
- Based on Lean pillars and principles
- Based on the Agile manifesto
- Doesn’t have a strict set of roles typical for Lean
- Has a list of specific roles and structured meetings that must be implemented
- Usually applied to entire organizations to make all processes more efficient
- Can be applied to individual projects
Advantages and Disadvantages of Lean Methodology
Lean is a very successful methodology that gained worldwide fame for a reason. It’s very flexible and adaptable, but as with any other management method, it has its perks and faults. Compared to other methodologies, it’s the only one that focuses so much on reducing waste, which mainly leads to cost reduction and, consequently, an increase in profitability. By comparison, Six Sigma focuses on defect reduction and traditional project management on project phases and how to complete them successfully.
The Lean strategy focuses on the customer throughout the process, similar to the approach of holistic marketing, which can be very beneficial both to the market as well as the efficiency of all company activities. Employees should also be happier as their efforts won’t be wasted on time-consuming, pointless tasks, and their opinion should be heard so the Lean process can be continuously improved. Implementing Lean, however, could be stressful to teams, and constant change for the better can create a sense of insecurity.
The initial introduction of the Lean philosophy can be quite costly and confusing to both managers and team members. It doesn’t help that it’s not a precise framework but rather a mindset without structure or strict guidelines on managing a project. The focus on efficiency and waste reduction can lead to forsaking long-term goals and missing out on some investments that might not seem as efficient and productive in the present.
Nevertheless, Lean is very useful when applied to manufacturing and can improve product quality significantly and shorten lead times. Its principles can improve the process in other industries, but managers should test out how the implementation affects productivity, employee satisfaction, and customer values.
ActiveCollab and Lean
ActiveCollab is a project management software that can easily and efficiently be combined with various project management methodologies. Using the ActiveCollab tool with Lean project management methodology can improve the processes and make them more flexible. ActiveCollab allows project managers and team members to have a complete understanding and an overview of all the projects and tasks the team is working on. By using ActiveCollab, project managers can easily and adequately distribute tasks across the team, making sure no one burns out using the Workload feature. They can also easily spot unused talent and eliminate waste to make the project more efficient and manageable. ActiveCollab is an easy-to-use project management tool that offers tons of possibilities for efficiently and effectively managing projects.
Continue reading
Project Management Methodologies Introduction
Get familiar with the most popular methodologies modern project managers use! Learn the basics and choose the best method to manage your teams and projects.
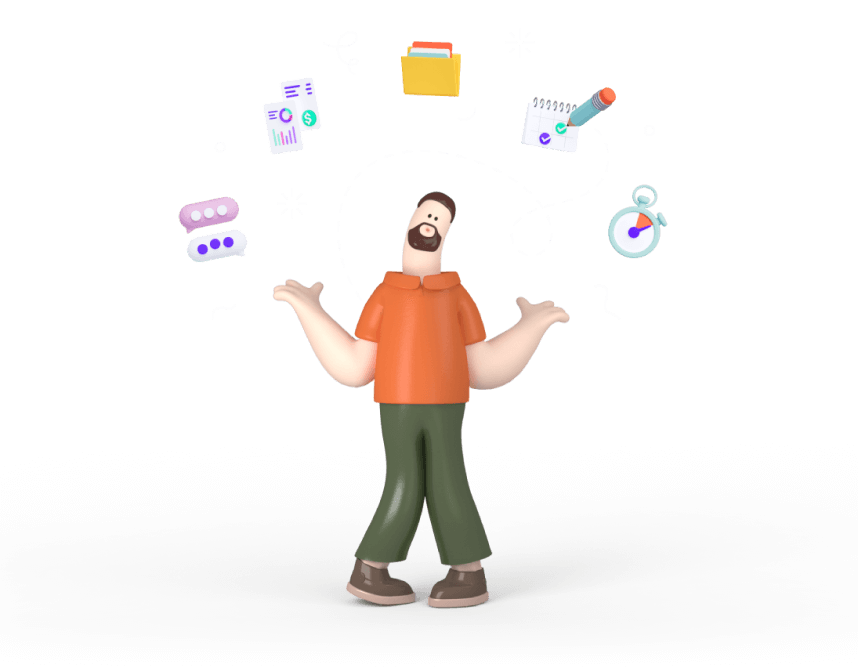